Voltamos à fábrica da SAAB no Brasil para ver a montagem de aeroestruturas do Gripen
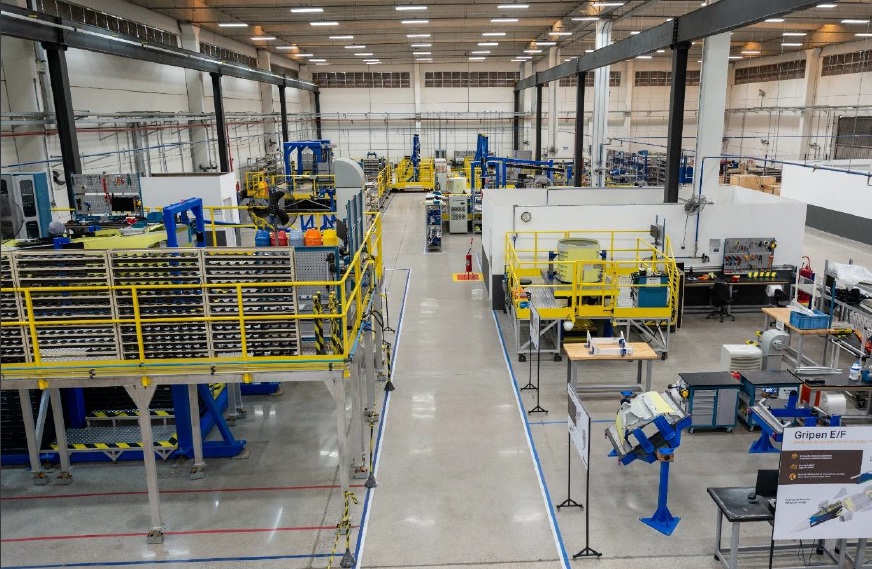
Além da produção de partes da fuselagem e asas de caças Gripen do Brasil e da Suécia, instalações incluem novos laboratórios para manter radares e sistemas de guerra eletrônica das aeronaves destinadas à FAB, além de outros equipamentos
Por Fernando “Nunão” De Martini
Três anos e sete meses atrás, o Poder Aéreo foi à apresentação do edifício da Saab Aeronáutica e Montagens – SAM, na cidade de São Bernardo do Campo (SP), numa concorrida coletiva de imprensa. A reportagem sobre aquela visita feita em 9 de maio de 2018 começou com a frase “um galpão industrial, novo em folha, chama a atenção por ainda se encontrar vazio de máquinas e de pessoal.” Há exatamente uma semana, na última quinta-feira, 9 de dezembro de 2021, tive a oportunidade de voltar à planta da Saab na cidade e ver o mesmo espaço finalmente ocupado por ferramental, equipamentos e pessoas produzindo no Brasil as aeroestruturas prometidas anos atrás, atendendo assim a um dos objetivos do programa de aquisição de 36 aviões de caça F-39 E/F Gripen pela Força Aérea Brasileira (FAB). E vi também uma novidade que não estava nos planos apresentados na ocasião: um laboratório para manter os radares e sistemas de guerra eletrônica dos aviões Gripen da FAB.
Se em 2018 superestimei o trânsito para chegar ao local e, bem adiantado, pude calmamente observar o galpão antes de ser ocupado por uma centena de convidados, desta vez subestimei o tráfego (e a quantidade de obras viárias no caminho) e me atrasei. Cheguei quando já havia começado a fala do novo diretor geral da planta da Saab em São Bernardo do Campo, Fabricio Saito. De cara, no pequeno auditório, pude perceber outro contraste com o lotado evento de caráter institucional de anos atrás: a presença de apenas uma dúzia de jornalistas.
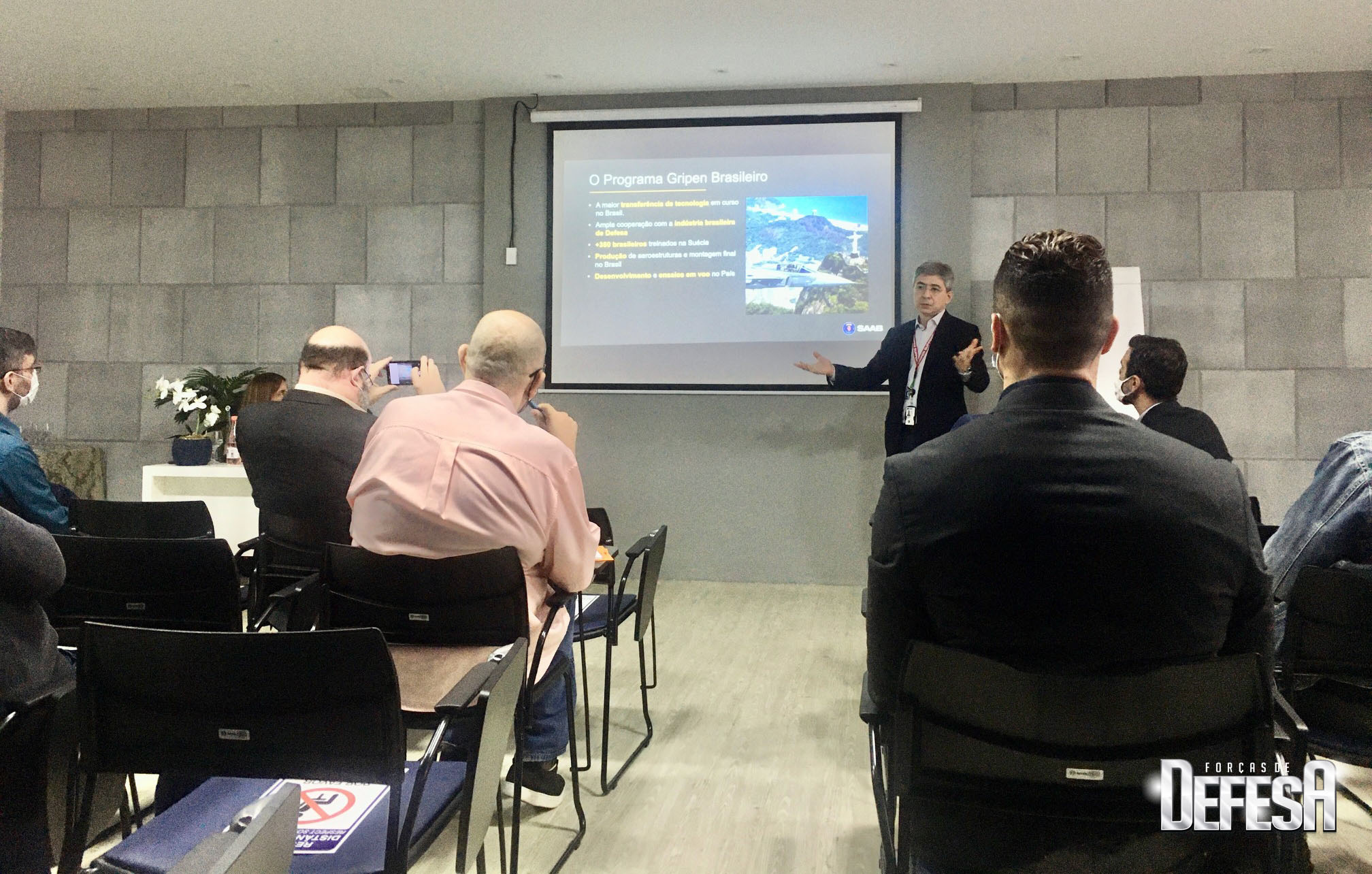
Mas os menos numerosos convidados de agora puderam conhecer um conteúdo bem mais extenso e real do que no evento de 2018, quando apenas totens de realidade virtual, telas e banners mostravam como seria a montadora de aeroestruturas. Como boa parte dos leitores do Poder Aéreo gosta de imagens e relatos de “chão de fábrica” do setor aeronáutico (chão bem limpo, nesse caso) desta vez poderão ver bem mais realizações do que promessas, ao mesmo tempo em que conferem alguns dos pontos principais das apresentações feitas pelo diretor geral Fabricio Saito, pelo gerente de engenharia (do setor de aeroestruturas) Alexandre Barandier Barbosa e pelo gerente de operações da Saab Sensores e Serviços, Gustavo Alves. E também as impressões deste colaborador do Poder Aéreo ao percorrer as estações de trabalho da SAM e o novo laboratório de manutenção de radares e sistemas de guerra eletrônica, que além de equipamentos do Gripen atenderá à demanda de manutenção de radares meteorológicos.
A SAM e as questões da indústria de defesa no Brasil: controle e transferência de tecnologias
Felizmente o atraso ao evento me fez perder apenas o café e os minutos iniciais em que o novo diretor se apresentou. Para suas credenciais, recorro então ao release da assessoria de imprensa: “Fabricio Saito tem uma carreira de 30 anos como engenheiro e diretor técnico de Manutenção na FAB e está na Saab há quatro anos. Formado em Engenharia Aeronáutica pelo ITA (Instituto Tecnológico de Aeronáutica) e com mestrado em Gerenciamento Logístico pelo Air Force Institute of Technology (AFIT), dos Estados Unidos, possui MBA em Gestão Estratégica de Negócios.”
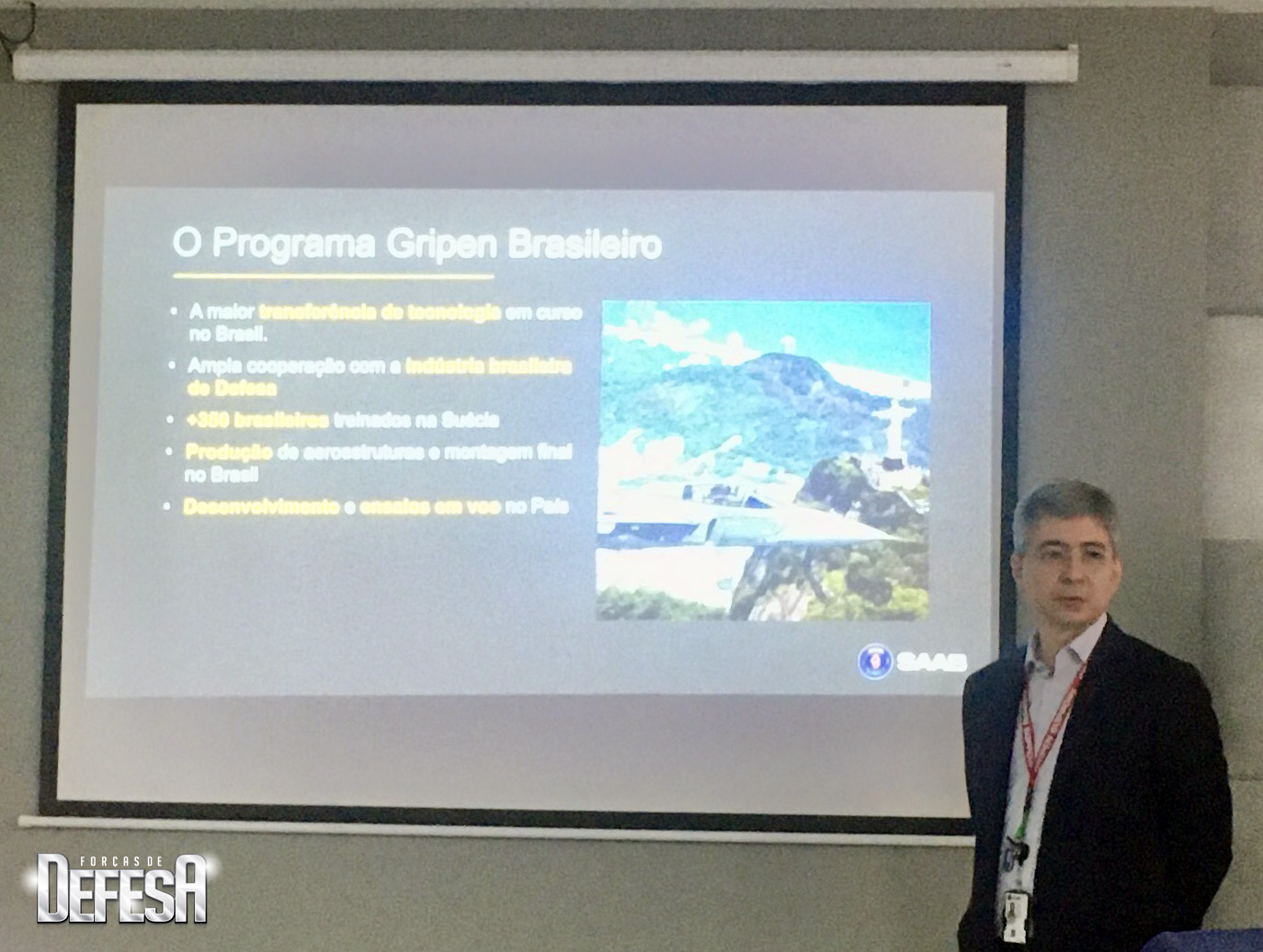
Com esse histórico de ITA e FAB, não é de estranhar que o diretor focasse boa parte de sua apresentação na capacidade da indústria aeronáutica brasileira em absorver tecnologias. Em especial, o fato desta ter partido praticamente do zero, nos anos de 1950, e hoje formar um complexo de empresas importantes local e globalmente. Em suas palavras, um “terreno fértil” para absorção tecnológica. O diretor considera que o programa Gripen é hoje o maior do Brasil em matéria de transferência de tecnologia, com mais de 350 profissionais brasileiros treinados na Suécia. A maior parte é da Embraer, mas neste número de 350 também entra a maioria dos 70 colaboradores da SAM, que treinaram na principal unidade fabril da Saab, na cidade sueca de Linköping.
A implantação da Saab Aeronáutica e Montagens (SAM) faz parte de um plano maior, em fases, iniciado em setembro de 2015 com a entrada em vigor do contrato da Saab com o governo brasileiro, no valor de 39,3 bilhões de coroas suecas visando o desenvolvimento e produção de 36 caças Gripen E/F, incluindo a transferência de tecnologia e o atendimento a necessidades específicas da Força Aérea Brasileira (FAB). Quando do anúncio da efetivação (10 de setembro de 2015), o valor correspondente em dólares, do contrato global, era de aproximadamente 4,7 bilhões, ou 18,2 bilhões de reais.
Apenas para efeito comparativo, ao câmbio de hoje as 39,3 bilhões de coroas suecas equivalem a cerca de 4,3 bilhões de dólares ou quase 24,5 bilhões de reais, devido à desvalorização da moeda brasileira (que já era um problema em 2015 e nos últimos anos agravou-se bem mais). A parcela desse valor que corresponde ao investimento direto da SAAB sueca na unidade de São Bernardo do Campo não foi revelada por Fabricio Saito, que não pode responder sobre o assunto especificamente – ainda que nós jornalistas insistíssemos no tema e ele exercesse considerável dose de bom humor para desviar das investidas. O diretor geral apenas se limitou a responder que o plano da Saab no Brasil é “sólido e duradouro” e que há uma determinação da empresa em fazer bom uso desse investimento para a continuidade dos negócios da filial brasileira.
Sobre o fato da SAM não ser uma empresa brasileira, pois acabou sendo viabilizada com 100% de controle pela Saab sueca (apesar de inicialmente terem buscado participação de capital nacional), este é um tema que sempre traz a discussão sobre a transferência de tecnologia se dar entre matriz e filial. O ponto de vista de Saito é que essa não é a questão principal. Para ele, o que mais importa é a empresa ser dirigida por brasileiros, com um grau de autonomia para atuar localmente, e que gere impostos e empregos no país. E, principalmente no caso de um setor de alta tecnologia, que esta seja absorvida por engenheiros e operários brasileiros.
Esta é uma discussão que permeia a própria história da indústria de Defesa no Brasil, e cabe ao leitor fazer sua própria análise a partir dos argumentos, ou, talvez de forma mais justa ou pragmática, a partir dos resultados práticos obtidos em cada caso. O fato que não se pode negar, e que este autor acredita ser premissa indispensável para qualquer discussão sobre o programa de caças do Brasil, é que hoje há efetivamente uma fábrica realizando a montagem de aeroestruturas de caças supersônicos país – resta saber se continuará viável daqui a alguns anos, a depender de novos lotes de caças Gripen para a FAB e de uso de sua mão de obra treinada, conhecimentos absorvidos e capacidade instalada em outros projetos.
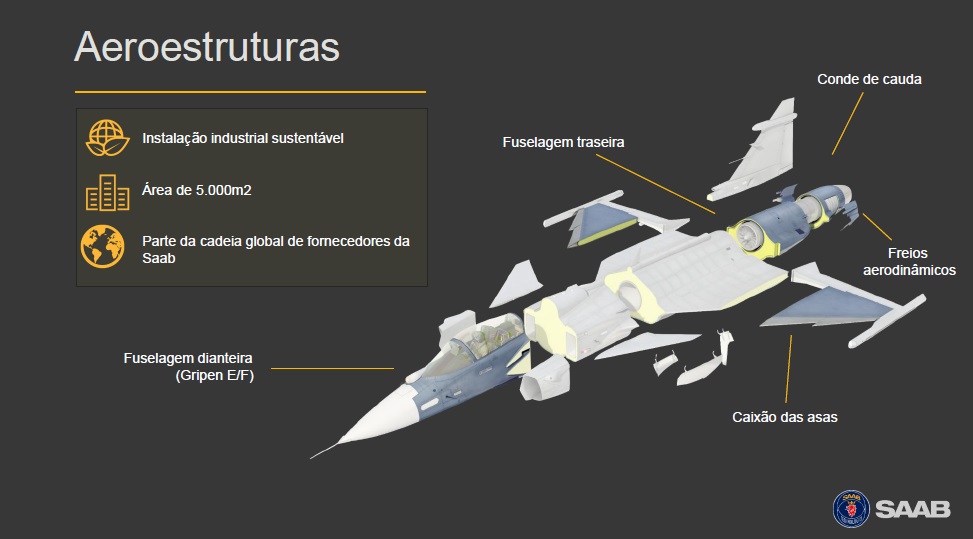
O diretor geral da planta de São Bernardo do Campo buscou, em sua apresentação, valorizar o fato de que, pela primeira vez no país, estão sendo fabricados segmentos aeroestruturais de boa parte da fuselagem e asas de caças supersônicos. Saito também ressaltou que as características das aeroestruturas de aeronaves supersônicas de combate, como o Gripen, são bem diferentes das empregadas nos aviões comerciais e subsônicos, sendo uma área ainda não dominada pela indústria aeronáutica brasileira. Vale lembrar que o projeto dessas aeroestruturas também teve importante participação de uma empresa do Brasil, a Akaer, mas esse é um assunto que foge ao objeto principal desta matéria, que é a fabricação.
Transferir tecnologia desenvolvida numa empresa estrangeira para profissionais de outra nação é um processo que envolve pessoas, com a absorção do conhecimento e sua utilização caminhando juntas. Saito também frisou que, para o processo funcionar, o destinatário deve ter capacidade de absorver (e a capacitação atingida pela indústria e engenharia aeronáutica brasileira permite isso), aplicar e tomar decisões no ambiente local. Neste caso, não apenas seguindo o projeto vindo da Suécia para utilizar os aportes financeiros diretos da Saab, mas adaptando os processos à produção no Brasil – a obrigação é que o produto final seja idêntico ao fornecido pela Saab, em Linköping, padrão que segundo a empresa está sendo cumprido e aprovado pela matriz.
Voltando à cronologia para encerrar esta seção e partir para questões mais técnicas, a seleção do caça sueco, dentro do programa F-X2 da FAB, foi anunciada em dezembro de 2013. Em seguida vieram negociações e cumprimento de condições solicitadas para que, em outubro de 2015, começasse efetivamente o programa de transferência de tecnologia.
Em 2016, quando o Poder Aéreo esteve em Linköping para a apresentação do primeiro protótipo do Gripen E, o tema da localização e dos prazos para instalar a fábrica de aeroestruturas no Brasil ainda estava em aberto. Numa das apresentações de cunho mais técnico feitas à imprensa daquela ocasião, especificamente sobre participação industrial, ao cobrar por informações a respeito de uma decisão sobre o tema (num ano conturbado na política brasileira) percebi que havia colocado um bode na sala. Nada poderia ser dito no momento. Só mais tarde as respostas vieram, com a definição de São Bernardo do Campo, seguida da concorrida apresentação do galpão industrial ainda vazio, em maio de 2018.

A fabricação efetiva da primeira aeroestrutura começou em junho de 2020, com o primeiro cone de cauda enviado à Suécia em dezembro do mesmo ano. A partir daí a produção e a complexidade foram gradualmente ganhando ritmo, com 5 dos 6 itens de segmentos aeroestruturais atualmente em montagem (fuselagem traseira, fuselagem dianteira do avião monoposto, caixões das asas, cone de cauda e freios aerodinâmicos), faltando ainda iniciar a produção da fuselagem dianteira do avião biposto. Mais detalhes à frente.
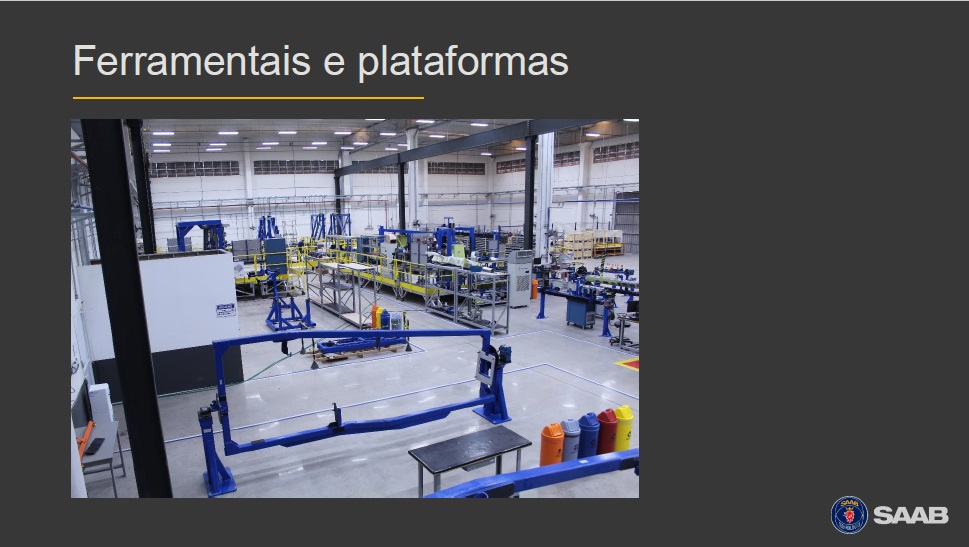
Ferramental produzido no Brasil
Partindo do tema da seção anterior para chegar ao chão de fábrica, um fato informado pelo diretor geral é que os engenheiros brasileiros responsáveis pela implantação da SAM, após o treinamento na Suécia, tiveram autonomia para projetar detalhes da unidade fabril brasileira a partir dos parâmetros estabelecidos pela matriz, o que incluiu a contratação do ferramental. Fabricio considera que a Saab é bem aberta em relação a preservar a autonomia local, o que inclui, desde o início da viabilização da fábrica, em manter a direção da filial de São Bernardo do Campo com brasileiros. O diretor acredita que isso sinaliza objetivos de longo prazo da empresa sueca no Brasil, um “plano sólido e duradouro” e não algo temporário ou restrito à produção das aeroestruturas já contratadas (traremos detalhes e quantidades destas mais à frente).
Sobre o ferramental, o gerente de engenharia Alexandre Barandier Barbosa informou que sua equipe de brasileiros participou plenamente da implantação e tropicalização dos ferramentais e plataformas da fábrica gerando confiança e autonomia. Todos os ferramentais (grosso modo, os suportes e gabaritos que são utilizados no processo de produção das aeroestruturas, vistos nas imagens desta matéria pintados na cor azul) foram encomendados a fornecedores no Brasil, numa seleção iniciada à época da inauguração do prédio em 2018. São equipamentos que devem obedecer a tolerâncias da ordem de centésimos de milímetros, e foi delegada à equipe brasileira da SAM o processo de selecionar e, em seguida, acompanhar a produção do ferramental por estes fornecedores, assim como a instalação, calibragem e aceitação, para enfim ter a aprovação final da Saab sueca e iniciar a produção.
Algumas particularidades e diferenças foram levadas em consideração. No galpão industrial sueco, por exemplo, as plataformas que sustentam o ferramental e trabalhadores são fixas no chão, enquanto nas instalações de São Bernardo do Campo elas são móveis (mas com suas rodas devidamente travadas), já pensando em maior flexibilização da planta industrial. Essas diferenças serão mais perceptíveis em imagens mais à frente. A média da temperatura ambiente da fábrica brasileira também é alguns graus mais alta do que a sueca, o que decorre das próprias diferenças de clima entre os países, fator também é levado em conta na calibração do ferramental e equipamentos de produção. Para isso, também foi instalada na SAM uma área dedicada a aferir e calibrar todo o ferramental, atendendo a um planejamento de manutenção.
Materiais suecos, produção brasileira de aeroestruturas
Se o ferramental, equipamentos de produção e a mão de obra são do Brasil, em compensação vêm de fora do país os diversos painéis, perfis e até mesmo certos subconjuntos que são recebidos, preparados, unidos e integrados na SAM, formando ao final do processo as diversas aeroestruturas de fuselagem e asa. Isso também inclui rebites, selantes e até as placas de materiais compostos.
O foco da empresa está no processo de montagem (daí seu próprio nome original, Saab Aeronática Montagens), e não no corte e dobra de metais ou produção de partes em material composto – neste último caso, um processo que demanda equipamentos caros como autoclaves para o “cozimento” de placas, que não teria viabilidade econômica neste momento em que a quantidade de asas encomendadas é pequeno. Ainda assim, trata-se de um trabalho bastante especializado e que requer precisão de centésimos de milímetros nos gabaritos e nas operações realizadas pelos operários.
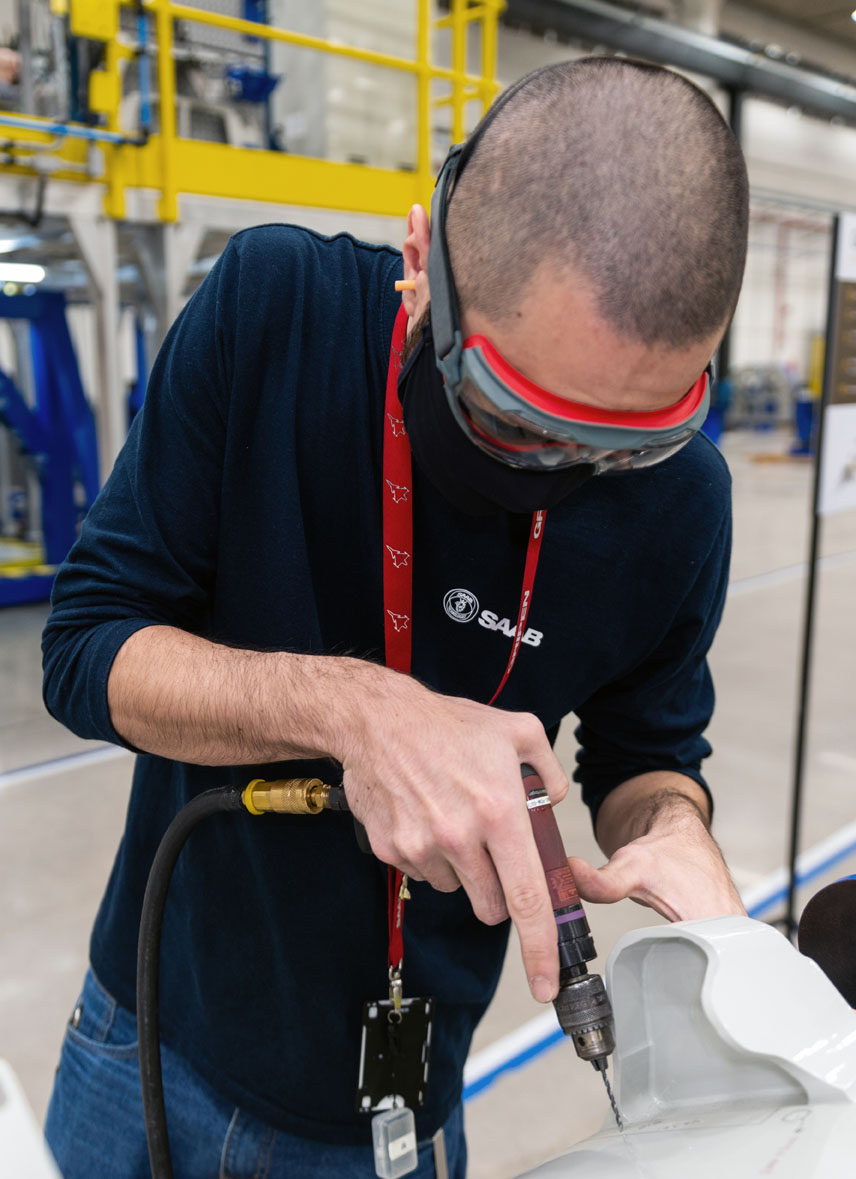
São seis os segmentos de aeroestruturas do Gripen que estão a cargo da SAM, dentro do contrato brasileiro: a fuselagem traseira, a fuselagem dianteira do Gripen E (monoposto – de um lugar), a fuselagem dianteira do Gripen F (biposto – de dois lugares), o caixão das asas (esquerda e direita), o cone de cauda e os freios aerodinâmicos (esquerdo e direito). Destes, cinco estão atualmente em produção, excetuando-se a fuselagem dianteira do Gripen F. Perguntamos quando deverá ser iniciada a produção deste segmento em especial, mas a resposta foi a protocolar dos casos em que esta não pode ser informada, e a qual estamos acostumados e não é incomum na indústria de Defesa: “conforme o cronograma estabelecido”.
No quadro abaixo está a relação dos segmentos de aeroestruturas e dos materiais de cada um (alumínio, metal duro e compósitos), assim como a quantidade contratada – no caso de produtos como o cone de cauda, o número a ser produzido é superior ao dos 36 caças Gripen encomendados pelo Brasil, dentro do objetivo original de inserir a SAM na cadeia global de fornecedores da Saab para a fabricação da aeronave. Para outras, a quantidade é menor devido à necessidade de se atender ao cronograma de entregas à FAB, portanto, serão fabricadas na Suécia para parte dos exemplares, e no Brasil para outra parte. Isso inclui a fuselagem dianteira do Gripen F, atualmente encomendado apenas pela FAB (por enquanto, a Força Aérea Sueca possui grande quantidade do biposto da geração anterior, o Gripen D, para atender às suas necessidades de conversão operacional de pilotos para o Gripen, o que é ainda a principal função de um biposto na doutrina daquela organização). A produção contratada na SAM será de 4 fuselagens do Gripen F, enquanto a FAB deverá receber oito exemplares desse biposto.

A expectativa da direção da SAM é que eventuais novas aquisições de caças Gripen E/F por Brasil e Suécia ampliem a quantidade a ser produzida de todos os 6 itens a cargo da filial brasileira, assim como possíveis contratos de outros países, a depender das propostas de cada um para participação na produção do caça. Infelizmente, no último dia 10 (apenas um dia depois da nossa visita à SAM) um dos potenciais futuros clientes do Gripen E/F, a Finlândia, escolheu outra aeronave: na disputa final de seu programa de 64 caças, onde após a eliminação de outros concorrentes sobraram apenas o sueco Saab Gripen e o Lockheed Martin F-35A dos Estados Unidos, o martelo foi batido para o avião americano. Mas ainda há concorrências em curso no mercado global de caças em que a nova geração do Gripen está bem posicionada como competidor. A conferir.
Andando pela fábrica: as partes já produzidas e o espaço para a próxima
Boa parte das informações expostas acima foi obtida durante as apresentações no pequeno auditório da SAM, outras tantas durante a visita às estações de trabalho dentro do galpão industrial, e reservo mais algumas destas para o rápido roteiro de imagens abaixo, junto com os leitores, especialmente as relacionadas a mais detalhes técnicos. Fotos não foram permitidas durante a visita à fábrica (apenas no auditório), assim as imagens do interior do galpão são as que a Saab forneceu após o evento. Porém, o Poder Aéreo aproveitou para acrescentar a elas algumas reproduções das telas das apresentações, também disponibilizadas após a visita, assim como as imagens de visita feita pelo site em 2019 às instalações da Saab em Linköping, onde foi permitido tirar fotos (de autoria do editor Guilherme Poggio), para comparações. A origem de cada uma das imagens está identificada abaixo das mesmas. Vamos à visita.
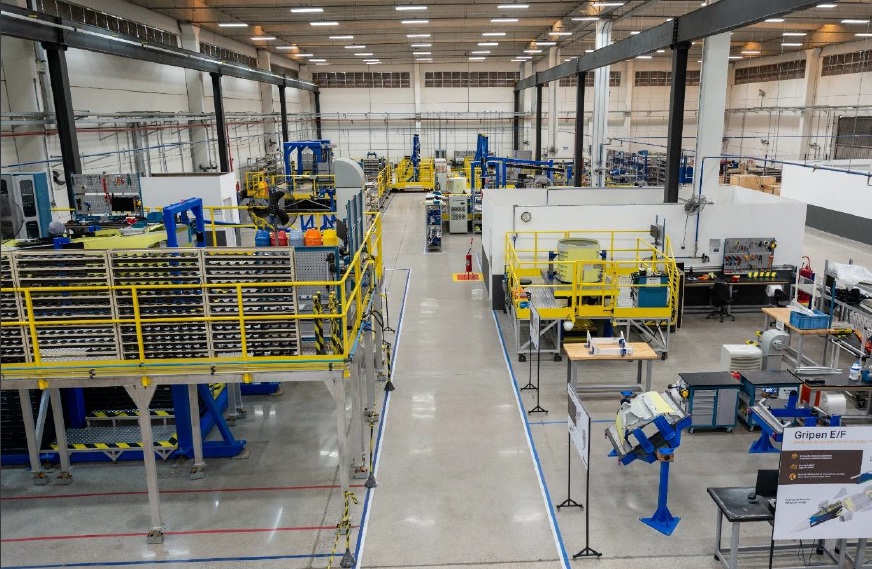
A área do empreendimento é de 5.000 metros quadrados, e parte foi ocupada pelos laboratórios de manutenção de radares, tema do final desta matéria. A organização é diferente de uma linha de montagem de produção em massa, como por exemplo da indústria automotiva, em que os produtos seguem um caminho em que partes são acrescentadas e processos realizados até chegar ao produto final. Na SAM, ainda que haja uma área em que são realizados sequencialmente os trabalhos de furação e união de peças, formando subconjuntos, cada um dos cinco segmentos aeroestruturais tem sua própria estação de produção. Como já mencionado acima, o ferramental (com pintura azul) e as plataformas dessas estações foram produzidos no parque industrial brasileiro, seguindo as especificações suecas com as adaptações da equipe de engenharia do Brasil.
Nestas estações, que incluem plataformas móveis para dar maior flexibilidade à planta industrial frente a futuras necessidades, todas as partes são unidas até formar o conjunto completo num só local, quando então começa a produção do próximo. Ou seja, diferentemente da linha de produção em que o produto se move até ficar pronto, neste caso o produto fica parado num local até que todas as suas partes sejam integradas do início ao fim. Isso não é incomum na indústria aeronáutica mesmo nas instalações de montagem final de aeronaves (que são as plantas que recebem os segmentos aeroestruturais como os produzidos na SAM), que em muitos casos se dá em baias ou posições estáticas individuais, ao invés de uma linha contínua. É um trabalho de atenção total à peça em fabricação, em que os operários especializados é que se movem em torno da mesma, que fica firmemente posicionada pelo ferramental e gabaritos (o qual permite, conforme o caso, que a peça seja reposicionada em dado momento para facilitar os processos).

Começamos a caminhada pela área dedicada aos freios aerodinâmicos, que são as partes menores e relativamente menos complexas de todas as produzidas, e que utilizam alumínio aeronáutico. Apesar da complexidade menor em relação a outras partes, são itens que em seu funcionamento no caça, em voo, terão que resistir a grandes forças aerodinâmicas, com altas cargas incidindo em suas superfícies e estruturas.
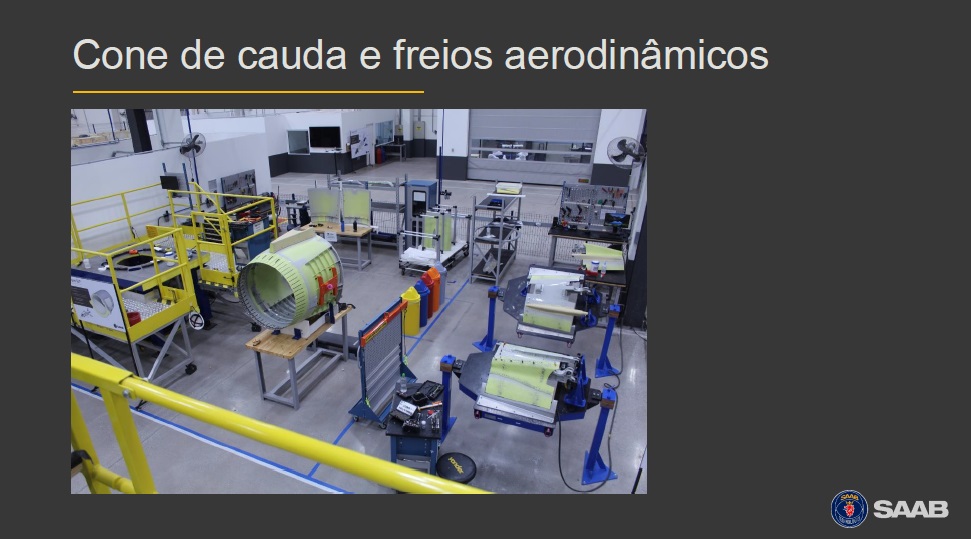
Segundo o gerente de engenharia Alexandre Barandier Barbosa, as peças e painéis recebidos da Saab sueca têm apenas alguns furos guia já feitos, sendo os demais realizados na SAM. Basicamente é um trabalho de precisão em furar, posicionar e unir partes com utilização de rebites aeronáuticos, mas cada um desses processos tem sua particularidade, para não falar de cada parte a ser unida.
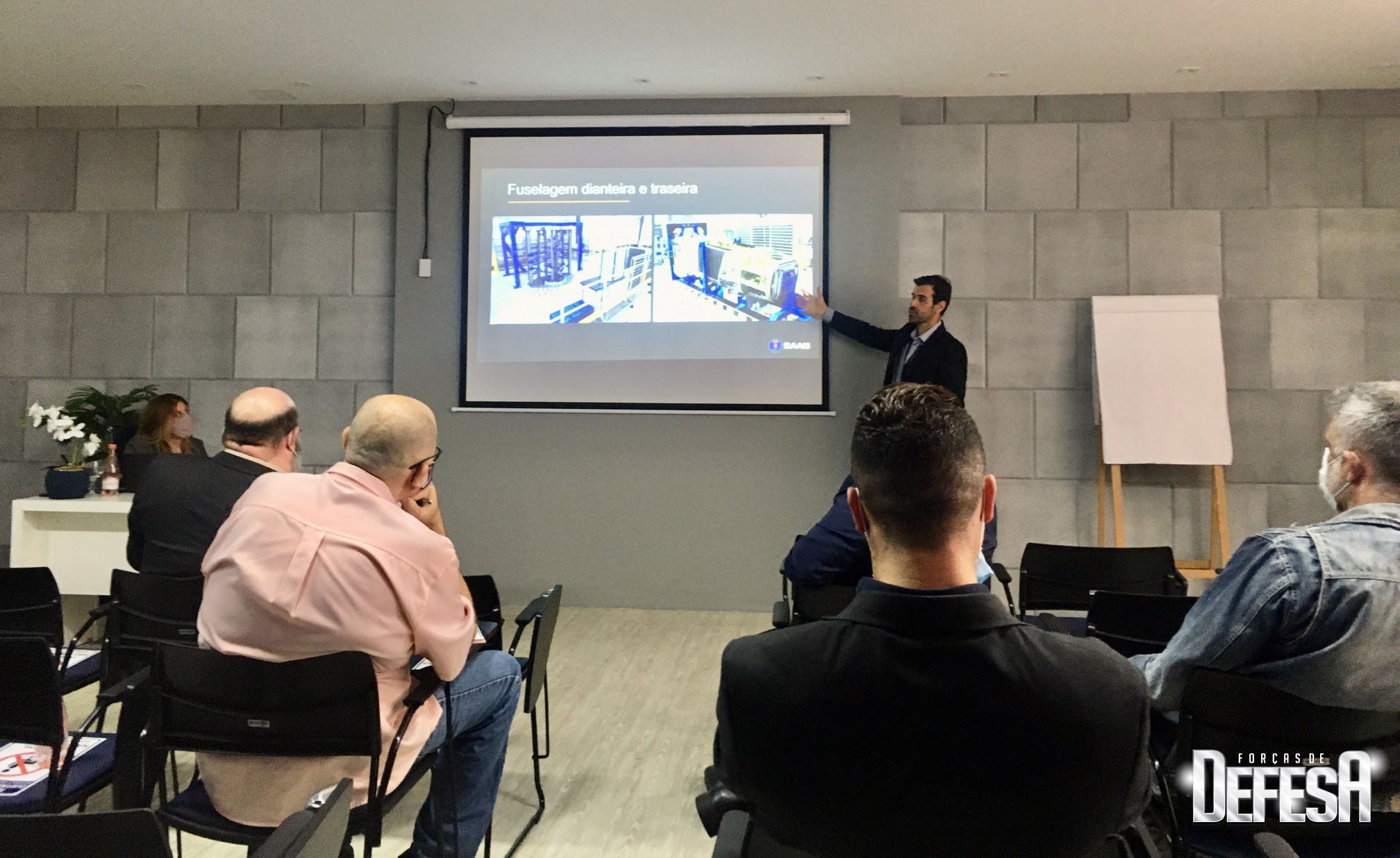
Os detalhes de cada uma das milhares de peças que compõem a fuselagem e superfícies alares de um caça Gripen são acessíveis por estações de computadores em cada estação, já que a SAM segue o conceito de fábrica “paperless” (sem papel, em inglês). Os desenhos e especificações estão todos em formato digital, constituindo imagens tridimensionais em que se pode destacar cada pequena parte. O sistema permite atualizar processos e desenhos de forma mais ágil em todas as estações da fábrica e entre as fábricas, no Brasil e na Suécia, assim como entre os centros de desenvolvimento do Gripen, numa rede própria.
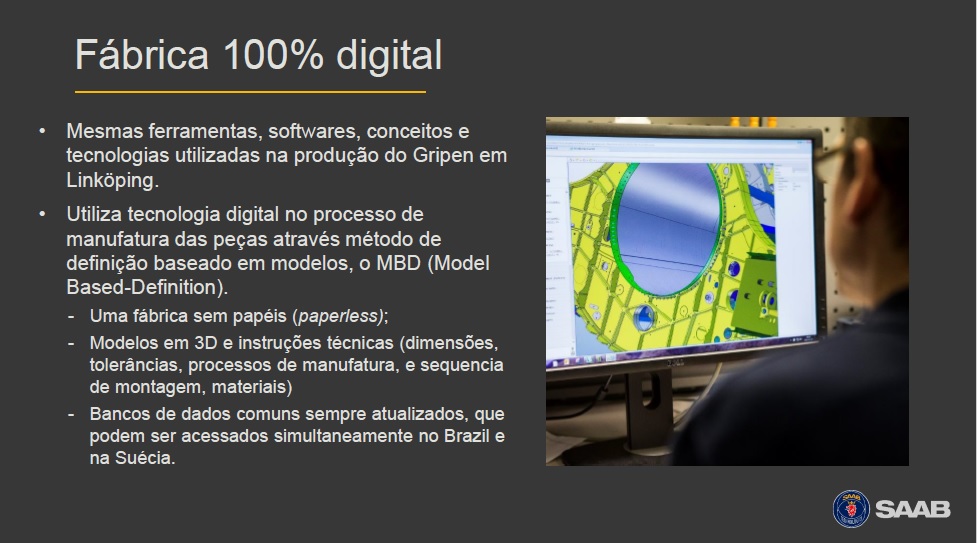
Na estação dos freios, estavam trabalhando junto aos funcionários brasileiros dois dos chamados “expatriados” suecos, empregados da Saab que garantem a continuidade da transmissão do conhecimento ao pessoal do Brasil que treinou em Linköping. Ambos tinham, cada um, cerca de 40 anos de experiência no setor. Seguimos para a estação dos cones de cauda, bem ao lado, o que é adequado: no avião, quando pronto, cone e freios ficarão juntos, sendo aqueles instalados nas duas laterais deste, na extremidade posterior do caça. Neste local, Barbosa aproveitou para apontar as rodas (com suas proteções e travas) na parte inferior da plataforma, que na fábrica da Saab na Suécia são fixas ao solo, como já foi mencionado mais de uma vez.
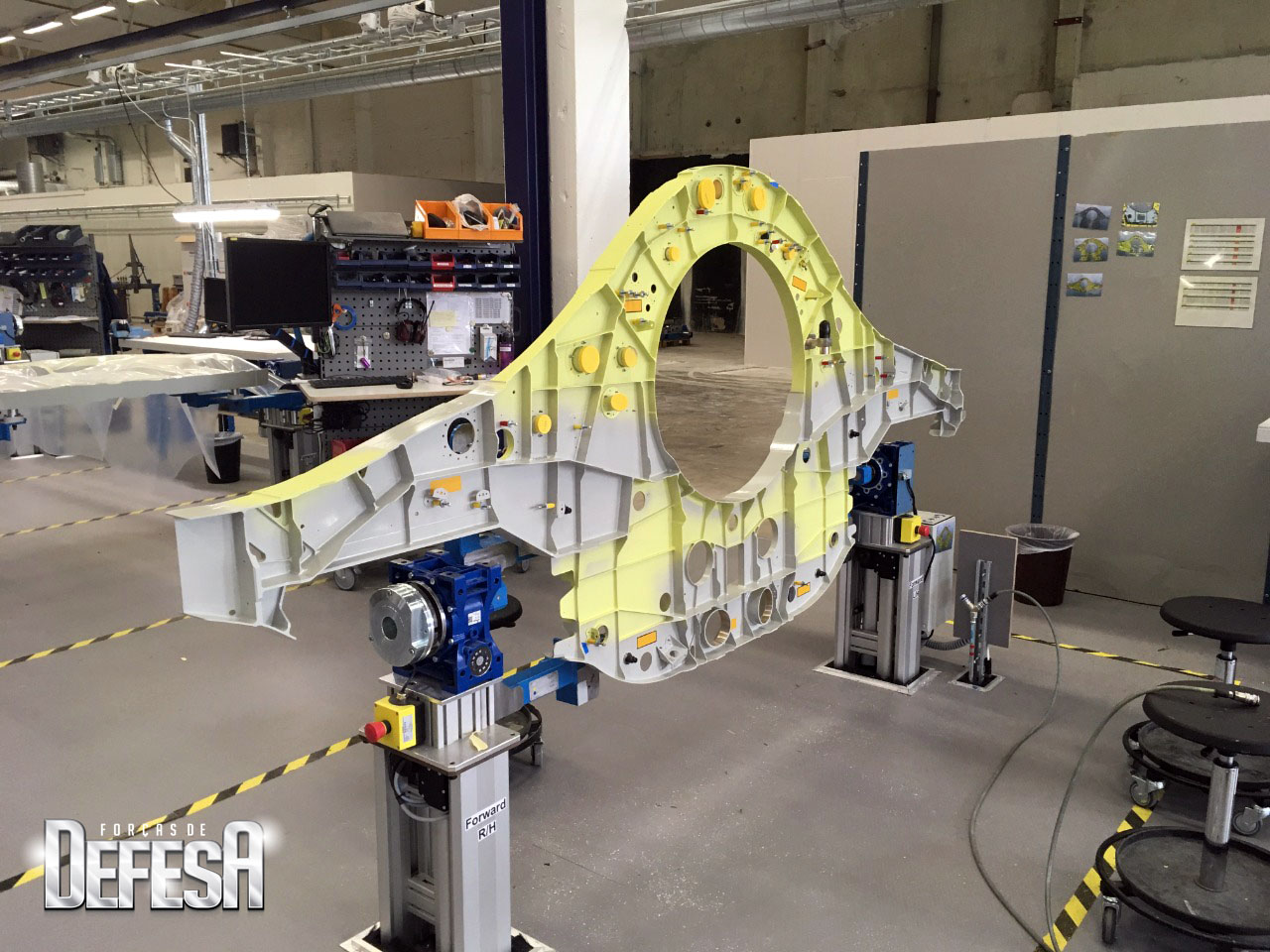
O cone é a aeroestrutura produzida na SAM que, além do alumínio aeronáutico, possui peças em metal duro (nome que na indústria em geral se dá a ligas de cobalto e tungstênio, que resultam num metal de alta densidade).
Do outro lado do corredor com as estações dos freios e do cone, está a plataforma que abriga o segmento aeroestrutural mais complexo pela quantidade de partes e processos que demanda, a fuselagem dianteira. Suas partes principais são os painéis laterais, que se conectam aos demais elementos estruturais e que também dão forma e sustentam os equipamentos que formarão a cabine do piloto. Ou dos pilotos, no caso do biposto.
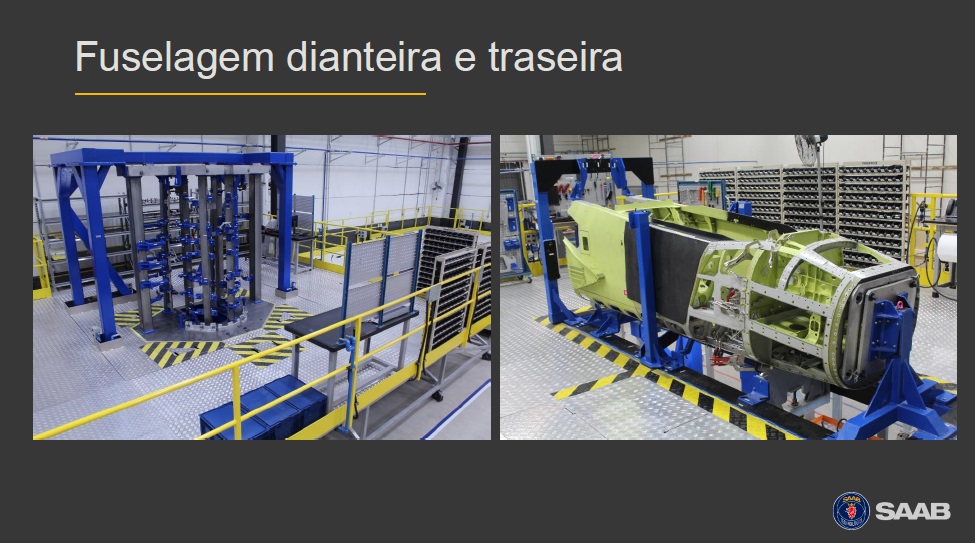
A área para futura instalação da estação em que serão produzidas as fuselagens do Gripen F, de dois lugares, está reservada ao lado, vizinha ao local onde foi erguido o laboratório de manutenção de radares. Será bastante semelhante à que produz a fuselagem do monoposto, segundo Barbosa e Saito. Na plataforma desta (imagem acima), pode-se ver o vão central da mesma, que facilita o acesso dos colaboradores à parte inferior da fuselagem em produção.
As superfícies pretas nas laterais da fuselagem são protetores dos painéis. Como essa fuselagem dianteira estava praticamente pronta, já era possível discernir, no que será o interior da cabine, os locais onde serão instalados o manete de potência, manche, assento, tela, entre outros itens do caça. Quando terminado, esse segmento estrutural, que é o de maior porte fabricado na SAM, precisa ser acondicionado numa caixa especial para envio à Suécia (e futuramente para as instalações da Embraer em Gavião Peixoto – SP, para as aeronaves que serão integradas no Brasil). Essa “embalagem” tem projeto sueco mas também contou com participação de brasileiros em sua concepção, segundo Alexandre Barbosa.
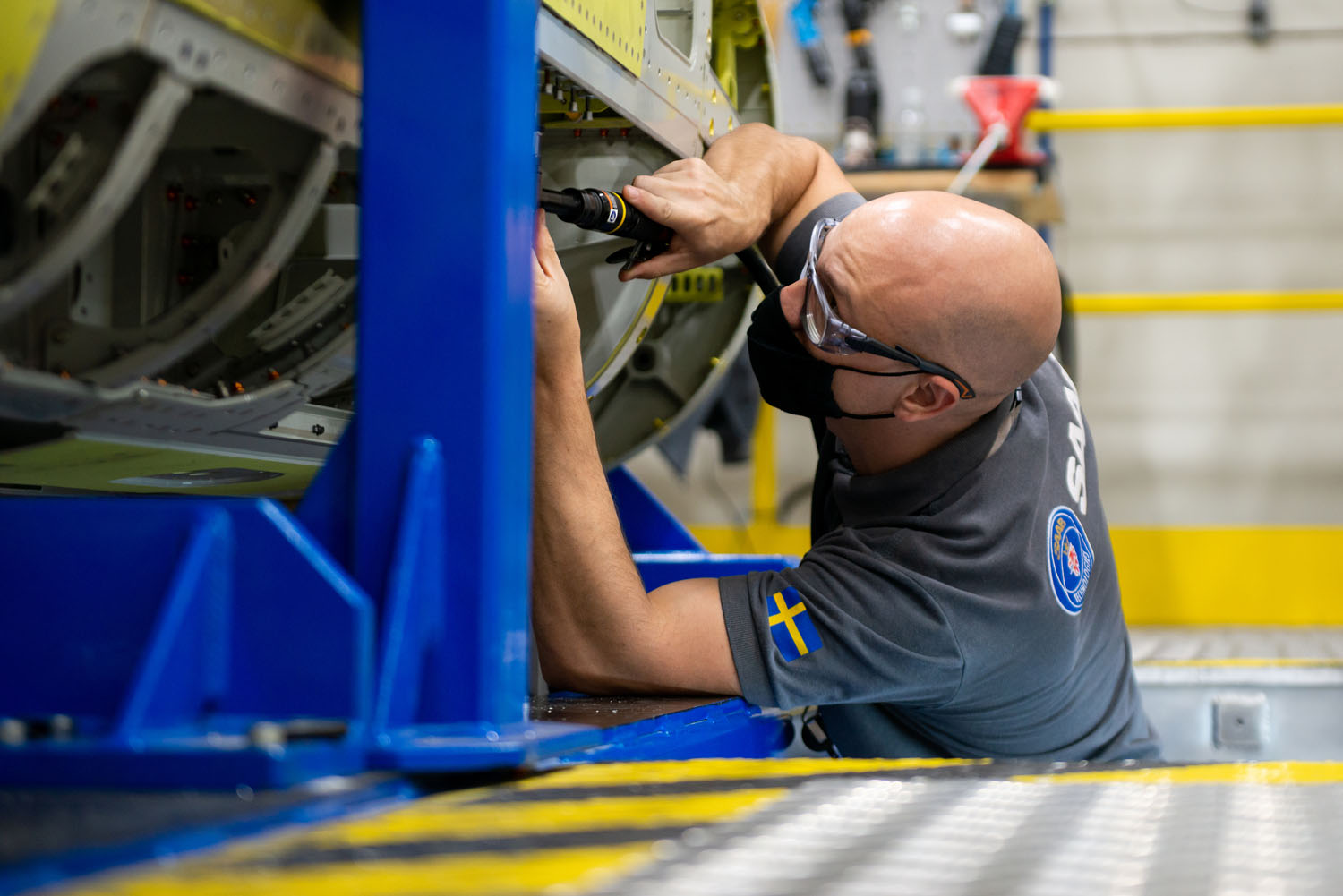
Prosseguindo em direção ao fundo do galpão, de um lado do corredor passamos pela estação de produção da fuselagem traseira, que é o segundo item que demanda mais peças e trabalho. Chama a atenção a disposição do ferramental, que permite a união das partes de uma aeroestrutura também complexa, em formato semicircular e que na aeronave acabada vai abrigar a maior parte do motor. Seu desenho faz a passagem das linhas da fuselagem com as das raízes dos bordos de fuga das asas. Do outro lado do corredor, a seção em que são preparadas e unidas as peças menores que atendem às demais estações (em especial, quanto à quantidade, as das fuselagens).
Chegando ao fundo, encontramos a estação que, para Barbosa, é a “menina dos olhos” da fábrica: a dos caixões das asas, cujos painéis e estruturas (incluindo as que sustentam os pilones / estações de armamento) são todos em material composto.
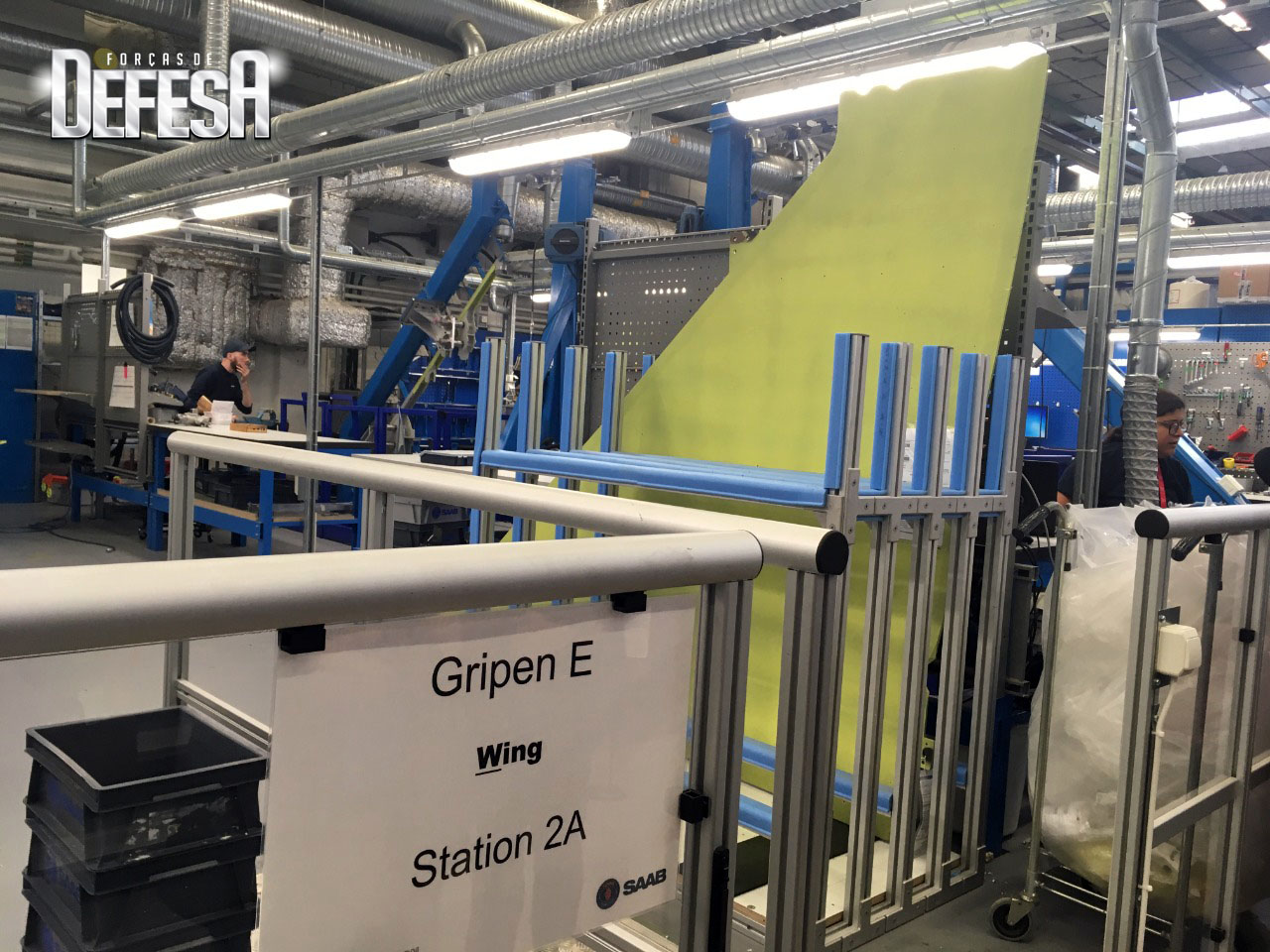
Basicamente, as peças estruturais são furadas e então rebitadas nos painéis de formato triangular que se dividem em quatro partes maiores, superior e inferior esquerda, e superior e inferior direita, que após suas uniões formarão as seções centrais da asa esquerda e direita. Dentro desses caixões de asas, é levada uma fração significativa do combustível do caça. Assim, essas aeroestruturas em material composto (cuja espessura é maior dos que a dos painéis de aviões comerciais) têm dentro de si tanto suportes grossos e aptos a grandes cargas (pilones a eles fixados levarão itens que superam uma tonelada de peso) quanto espaço útil para líquido, o qual não pode vazar pelas junções – material selante específico é empregado na união das partes.
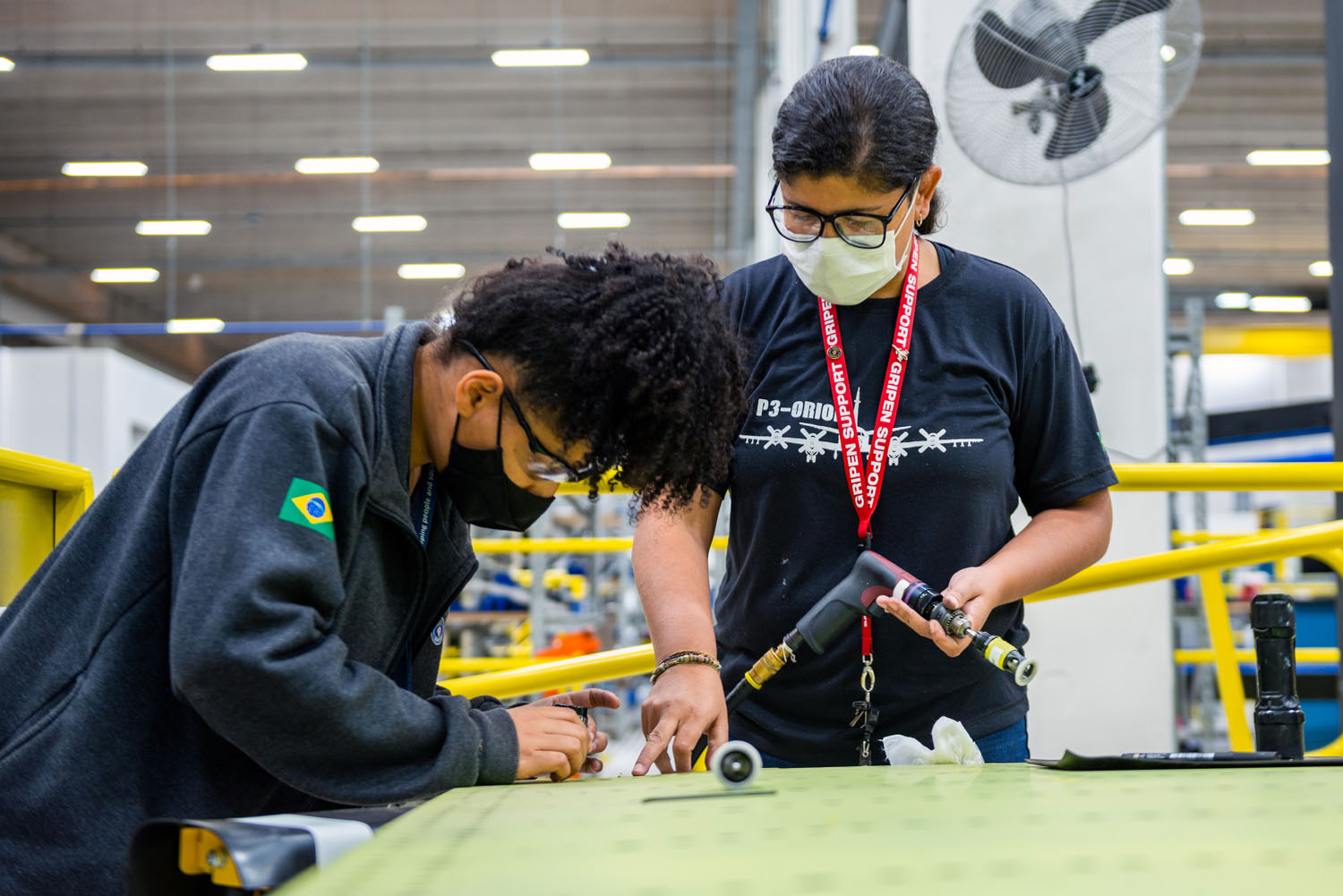
A estação dos caixões das asas é dominada por mulheres, que se sobressaem no treinamento para as operações com material composto, o qual demanda ainda mais atenção quanto a detalhes e cuidado. Ou seja, é o domínio da ala feminina da SAM na área alar do caça, com o perdão do trocadilho.
Terminando a volta pela fábrica, passamos pela seção que faz a manutenção e calibragem dos ferramentais, que tem uma porta corrediça que a segrega do resto do galpão. Apesar da visível robustez e rigidez do ferramental, o uso pode levar a pequenas deformações que precisam ser corrigidas pois, como já mencionado, as tolerâncias são da ordem de centésimos de milímetros. Ali também estava outro expatriado sueco, Ola Rosén, diretor de operações que além de “materializar a transferência de tecnologia”, nas palavras do diretor Saito, é também torcedor do Santos Futebol Clube. Pensei, com a autoridade a mim conferida por também ser torcedor do time, em fazer piada se os demais trabalhadores também seriam santistas, já que notei a pouca quantidade de pessoas trabalhando ao mesmo tempo na fábrica – é notório o contingente diminuto, hoje, de torcedores do Santos… Mas considerei que, assim como os produtos da fábrica, seria uma anedota de complexa compreensão, e até um pouco injusta para com a efetiva quantidade de trabalhadores da SAM: quando voltamos para o auditório após a visita, passamos em frente ao refeitório, e constatei que lá estavam vários dos trabalhadores que não vi nas estações de trabalho. Isso porque a fase inicial de apresentações do evento daquele dia acabou se estendendo e visitamos a fábrica bem mais perto da hora do almoço.
Ainda assim, é bastante comum ver relativamente poucos trabalhadores ao mesmo tempo numa instalação industrial de Defesa atualmente, com suas cadências de produção cada vez menores e complexidade maior de seus produtos, exigindo trabalho intensivo de menos pessoas. Enfim, foi mais sensato na hora apenas elogiar a excelente escolha de time que Rosén torce no Brasil. Na minha opinião de santista, é claro.
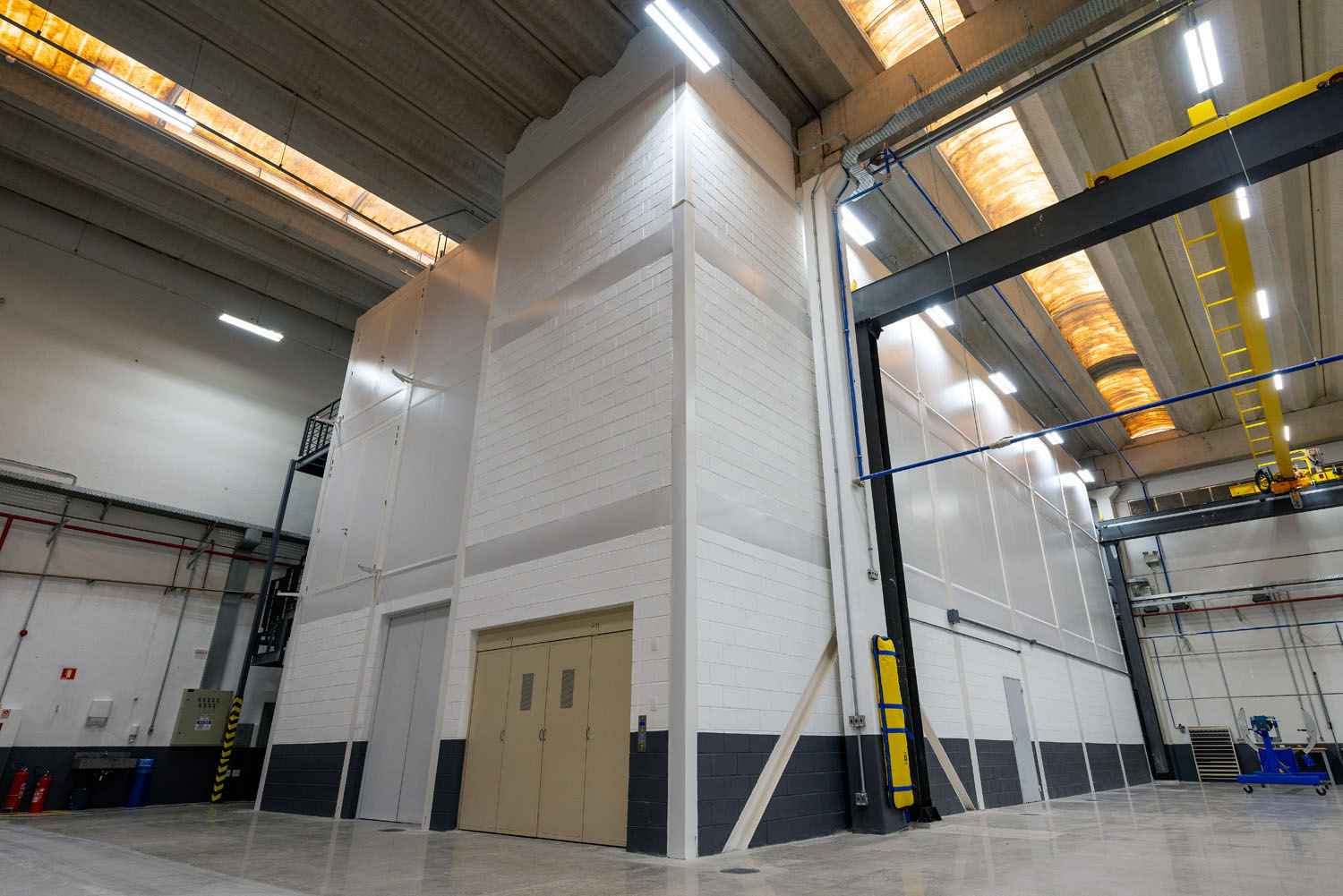
Novas frentes: laboratórios de manutenção de radares
A última área da fábrica que visitamos correspondeu também ao último tema da apresentação realizada pouco antes da visita, no auditório: o recém-construído laboratório de manutenção de radares e de sistemas de guerra eletrônica do caça, com área de 600 metros quadrados, no interior do galpão (a construção não existia no galpão quando foi visitado em 2018, sendo projetada e erguida especificamente para a finalidade).
Essa atividade, com o perdão de mais uma piada, não estava necessariamente no radar de atribuições da fábrica de São Bernardo do Campo quando de sua concepção, mas tornou-se uma necessidade com a aquisição da Atmos Sistemas pela Saab em abril do ano passado. A brasileira Atmos já era uma das empresas ligadas ao programa do Gripen no Brasil e possuía desde 2010, época em que o Gripen era ainda apenas um concorrente do programa F-X2 da FAB, um memorando com a então Selex Galileo (hoje no Grupo Leonardo) relacionado ao radar do caça, o Raven ES-05 AESA, de varredura eletrônica ativa. A Força Aérea Brasileira tinha entre suas exigências, no programa do Gripen, que os radares do Gripen não precisassem ser mandados fora do país para sua manutenção, dentro de uma perspectiva de 30 a 40 anos de operação dos caças. Assim a Atmos tornou-se, com a escolha do caça no programa F-X2, uma das parceiras do programa, coroando a decisão de anos antes em assinar um memorando com a Selex Galileo.
Além disso, a Atmos era responsável pela manutenção de radares meteorológicos, tarefa que, com a sua aquisição pelo grupo sueco em 2020, passou para a Saab Sensores e Serviços. Considerando que as instalações da Atmos necessitavam de expansão e modernização para atender a todas essas atribuições, decidiu-se instalar no galpão da SAM um novo laboratório, ou melhor, dois conjuntos de laboratórios: um para os radares e sistemas de guerra eletrônica do Gripen, outro para o apoio a um total de 13 radares meteorológicos operados (dos 27 que o Brasil possui) e eventuais outros negócios a serem trazidos para as instalações, dentro da especialidade de sistemas que utilizam tecnologia de microondas (não confundir com o eletrodoméstico).
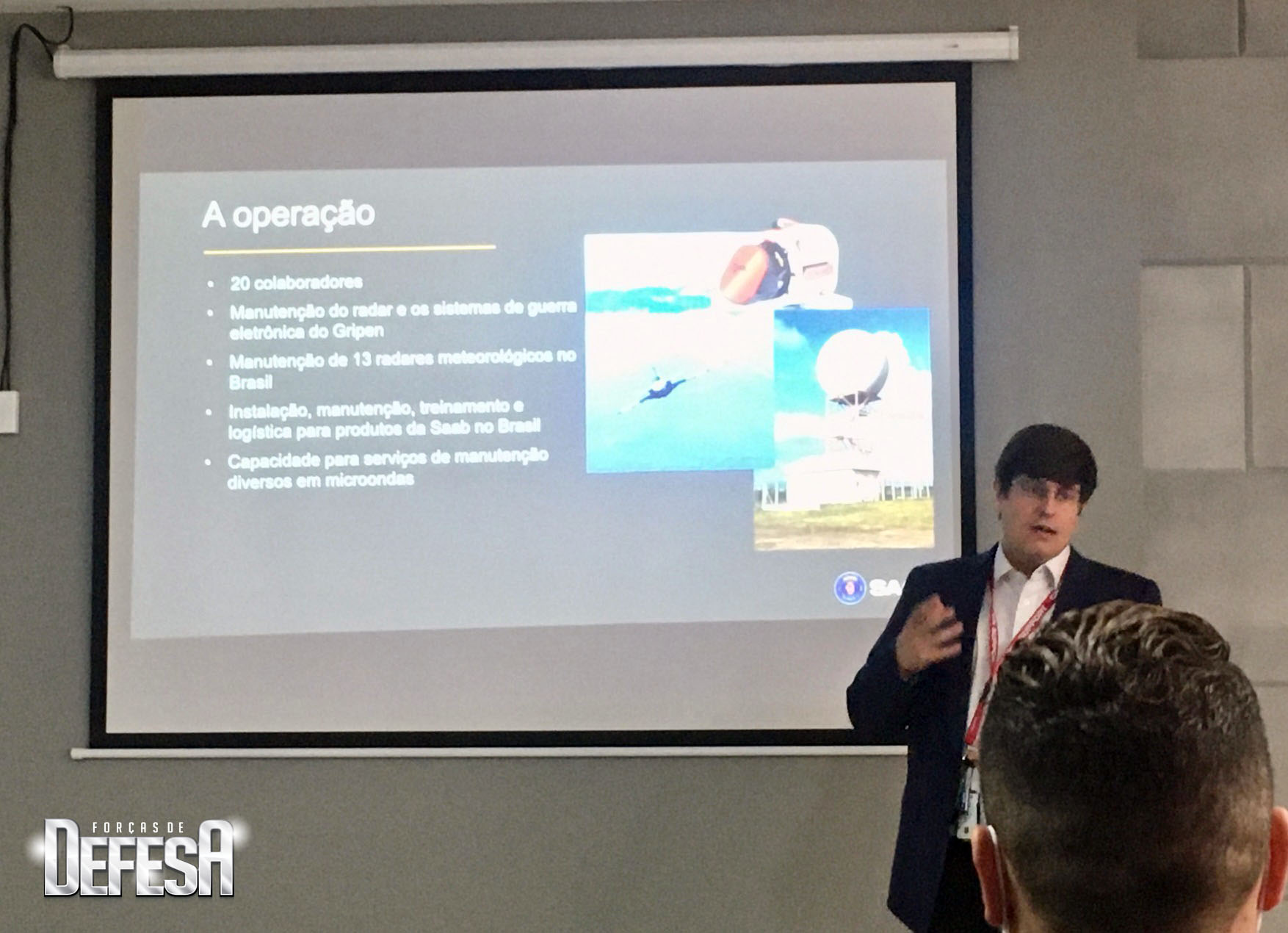
Segundo o gerente de operações da Saab Sensores e Serviços, Gustavo Alves, a mão de obra especializada provém da própria Atmos, mantendo os empregos da empresa adquirida. Ele também informou que a aquisição se deu pela Saab do Brasil, sendo uma empresa com CNPJ – Cadastro Nacional de Pessoas Jurídicas. Vinte colaboradores deverão trabalhar no local, que está com sua infraestrutura pronta e pudemos conhecer – neste caso, em espaços totalmente vazios, embora fotos disponibilizadas pela Saab e que usamos para também ilustrar esta seção (já que a captura de imagens não foi igualmente permitida no interior dos laboratórios), mostram alguns equipamentos dentro do laboratório. O efetivo apoio a esses sistemas do Gripen E/F no local deverá iniciar quando da entrada em operação do caça no país. Já a manutenção de 13 radares meteorológicos que são operados pelo CEMADEN (Centro Nacional de Monitoramento e Alertas de Desastres Naturais), pela Defesa Ciuvil de Santa Catarina e Agência de Águas de Pernambuco, já é realizada pela Saab Sensores e Serviços.
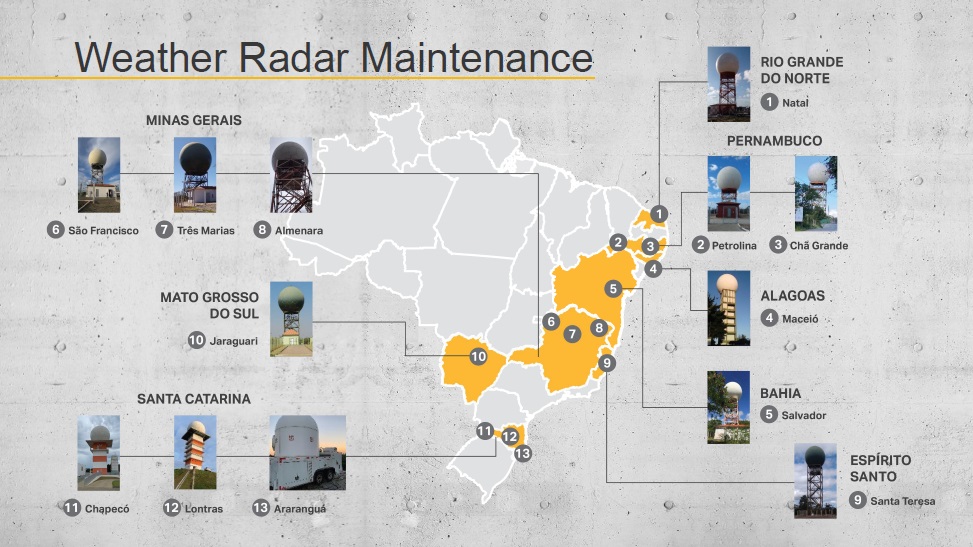
No caso dos radares e sistemas de guerra eletrônica dos caças Gripen da FAB, a implantação do laboratório segue três fases. A primeira foi a de transferência de tecnologia, a segunda é a atual, de construção do laboratório (atualmente recebendo os toques finais, assim como testes da infraestrutura, obtenção de licenças operacionais e elaboração de procedimentos operacionais), o que inclui a instalação dos equipamentos de teste (alguns já recebidos e ainda a serem instalados) e a terceira é a fase de execução da manutenção. Falando ainda da fase 2, as principais atividades para realizar nos próximos meses são a construção da bancada de testes (montagem, auto teste e validação), e de dispositivos de teste, no caso a construção do primeiro dispositivo de interface de Guerra Eletrônica (EW-ITA).
A bancada de testes do radar Raven, apesar de utilizar componentes e sistemas importados (segundo Alves eles já vieram e estão armazenados aqui) deverá ser instalada / montada inteiramente no Brasil. A Saab, segundo o gerente de operações, tomou uma decisão similar à relacionada à instalação do ferramental e plataformas da SAM: deixar com a equipe brasileira, após o treinamento na Suécia, a função de construir a bancada, ao invés de simplesmente importar uma pronta e colocar para funcionar, como uma “caixa preta”.
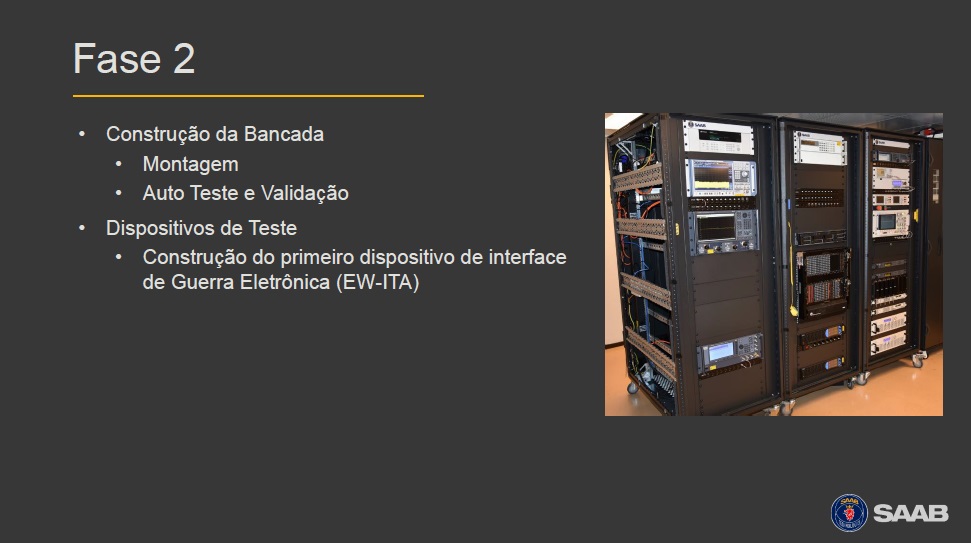
Na imagem acima, a bancada existente na Suécia, similar à que estará no laboratório dentro da SAM. Os diversos sistemas em manutenção, ao serem conectados à bancada, devem “entender” que estão em conexão com um caça Gripen, sendo igual no fornecimento de energia, troca de dados, resfriamento e outras funções, o que inclui similar condições de funcionamento em câmaras de teste ambiental (temperatura, pressão atmosférica), que não são vistas na foto. Gustavo Alves procurou destacar que a bancada é composta de equipamentos no estado da arte, tal como o radar Raven do Gripen e seus sistemas de guerra eletrônica.
Nas duas telas de apresentação a seguir, os equipamentos do Gripen que serão mantidos no novo laboratório e as capacidades de serviço das instalações:
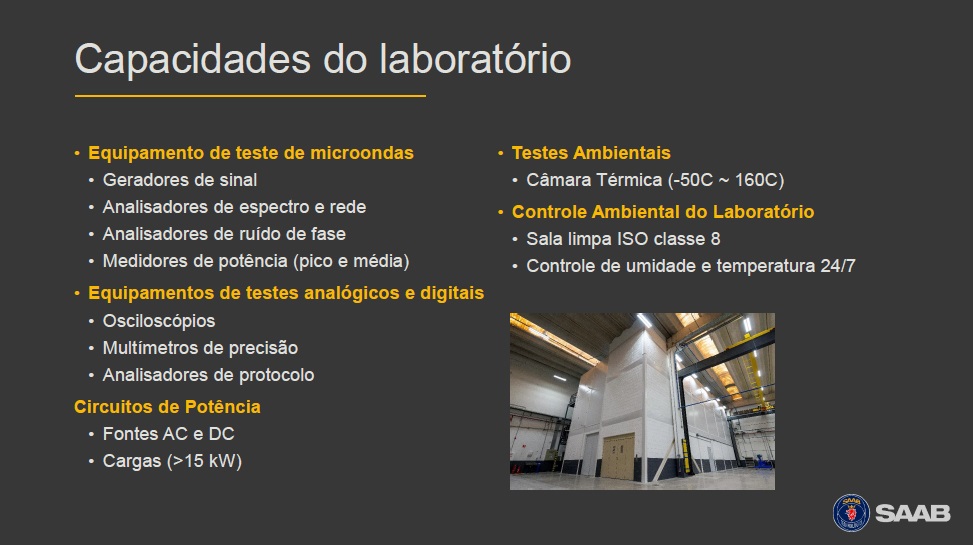
Visitando as diversas salas recém-construídas, percebemos uma separação entre as áreas: no piso térreo (contíguo ao da fábrica) está o conjunto de salas para a manutenção dos sistemas do Gripen. Nos andares superiores da construção, estão as salas para manter os radares meteorológicos e outros negócios, assim como depósitos de equipamentos de maior volume, estes no topo da área construída no interior do galpão.
Ambos os conjuntos seguem uma mesma ordem de salas, construídas e organizadas, em seus equipamentos de controle de temperatura e pureza do ar, para garantir sequencialmente um maior grau de eliminação de partículas que possam contaminar os equipamentos, a cada porta. A sala inicial é para recebimento e desmontagem dos sistemas, havendo também grandes portas para entrada de itens de maior porte. Daí se passa a salas de estoque de sobressalentes e à de efetiva manutenção dos equipamentos. Piso e mobiliário são especificados para reduzir possibilidade de geração de eletricidade estática, havendo também outras facilidades para isolamento e controle ambiental, instalação de água refrigerada industrial para resfriar os equipamentos, assim como itens de segurança dos trabalhadores. Tudo muito branco e asséptico ao olhar do leigo. Ainda vazio, como já foi um dia o chão de fábrica da SAM alguns anos atrás, mas que agora se encontra em atividade. Esperamos poder trazer, nos próximos meses, notícias sobre a instalação dos equipamentos no laboratório – a informação da Saab é que ele começará a funcionar em 2022.
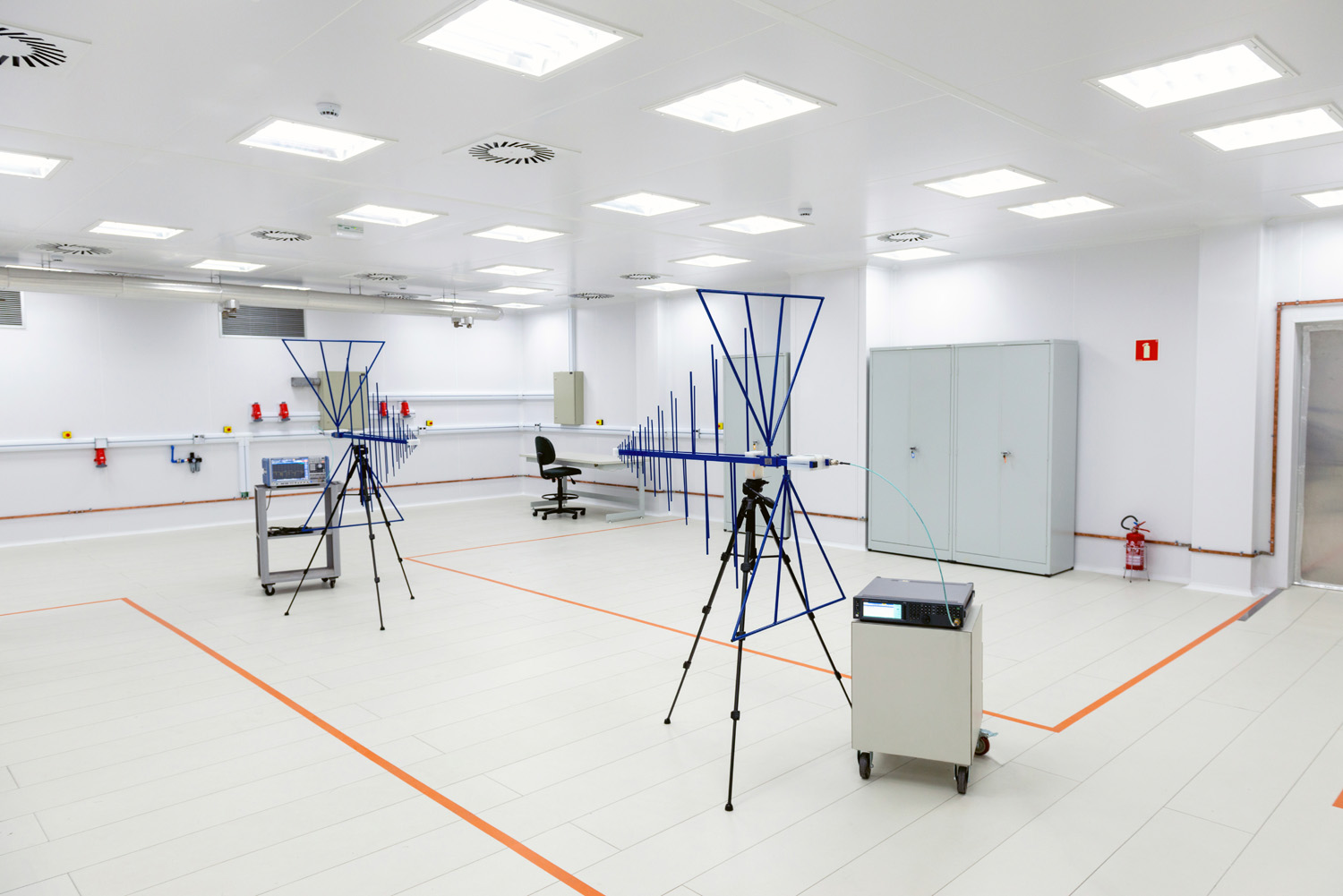
E falando em espaços cheios e vazios, o diretor geral Fabricio Saito foi perguntado sobre o que vem depois do Gripen (questão também em voga há três anos e meio ao seu predecessor, Marcelo Lima, o que levou à nossa reportagem anterior sobre a SAM a receber o título “Além do Gripen”). Fabricio respondeu que, dado o conhecimento gerado no trabalho de “tropicalizar” e adaptar a produção de aeroestruturas do caça, a SAM pode gerar “business case” para qualquer demanda em aeroestruturas, o que já tem para o caso de radares meteorológicos. Uma carteira de encomendas mais cheia tem sido sempre um dos principais obstáculos para a continuidade de diversas empresas ligadas ao setor aeronáutico e de Defesa no Brasil, sejam elas de controle nacional ou estrangeiro. E este é certamente um desafio para o braço brasileiro da Saab sueca, seja com a continuidade do programa do Gripen, seja além dele.
VEJA TAMBÉM:
- Saab Press Trip 2019 – parte 1
- Saab Press Trip 2019 – parte 2
- Saab confirma fábrica de aeroestruturas em São Bernardo
- Além do Gripen: Saab apresenta fábrica de aeroestruturas do caça, no Brasil, de olho no mercado mundial
- Além do Gripen – parte 2: conversa com piloto de provas da Saab e atualizações sobre o programa
- Conhecemos de perto o Gripen 39-7, avião de testes de sistemas da nova geração do caça sueco
- Roll out do Gripen E: vídeo da Saab e fotos do Poder Aéreo
- Apresentação do Gripen E: pausa para foto da imprensa especializada brasileira
- Agora é oficial: Selex Galileo assina memorando com a Atmos Sistemas
- Saab adquire a empresa brasileira Atmos Sistemas
- Brasil: parceria estratégica para a Saab
- O urso mora ao lado
- Press trip do Gripen brasileiro: faça sua pergunta
- Saab Press Trip: Gripen E Q&A
- Gripen E Q&A: versão não tripulada
- Gripen E Q&A: a pintura definitiva
- Gripen E Q&A: Gripen desdobrado na FAB
- Gripen E Q&A: e a versão naval?
- Primeiros Gripen E serão configurados apenas para missões ar-ar
- Uma fábrica subterrânea
- As chances do Gripen ao redor do planeta
- Vídeo: entrega do primeiro Gripen E brasileiro
- Poder Aéreo na Suécia
Parabéns pela matéria, Nunão. Muito completa e bem detalhada. Realmente poder realizar a manutenção em radar AESA no Brasil será outro nível.
Que matéria!!! Parabéns, é pra ser linda várias vezes. Precisamos de um governo sério que coloque em pauta a navalizacao do Gripen E/F, mesmo que seja para uso em bases litorâneas, com capacidade de resistir a intempéries de vôo de baixa altitude sobre o mar, precisamos.
Sabe o que eu pediria ?
Uma matéria dando maiores detalhes sobre essa recente alteração nas antenas das asas do nosso Gripen !
Em muitos sites por ai, estão afirmando que de trata de um belo downgrade (E imagino que possa ser por recente questões de custos, ja que chegaram a trocar a do 1o Gripen recebido).
Disseram que não temos S-400 ou SU-57 como ameaças… Então seria mesmo um sistema mais antigo ?
“Em muitos sites por ai, estão afirmando que de trata de um belo downgrade” Chris, com todo o respeito, mas isso você nem precisa ver em sites por aí, está claro que nosso sistema de EW é inferior ao Sueco, aquela desculpa que não temos S-400 e Su-57 como “inimigos” não faz o menor sentido, só os maiores passadores de pano que tentam explicar o inexplicável. É mais ou menos assim, eu tenho dinheiro e quero comprar um fuzil, eu só não compro porque os meus supostos inimigos tem apenas revólver e pistola, ai eu acabo comprando apenas uma pistola,… Read more »
Tbem penso assim…
Chris, pelo que eu entendi esse sistema é modular, “plug and play” ou seja, em caso de necessidade é só tirar um e conectar outro, como o Gripen foi projetado desde o inicio para ter essa modularidade os sistemas já estão todos disponíveis se necessário.
Como no momento não temos essa necessidade, realmente não faz muito sentido.
Seria mais ou menos como um morador do Piauí reclamar porque seu carro não veio com sistema de aquecimento dos bancos..
Mas seu nosso amigo piauiense for com seu carro para Curitiba no inverno, ele vai pensar muito. Graças a Deus que meu carro tem aquecimento de banco. Depende de onde você vai operar seu caça. E se por uma emergência precisar de equipamento e não tiver? Não se esquece de doutrina, não adianta mudar em cima da hora se o caçador não treinou com ele e não tem doutrina, logo em 7 segundo de combate se comete um erro de interpretação e lá se foi! Paguei caro por isso mesmo que não goste, quero pimenta, maionese e o escambau no… Read more »
Excelente matéria. Bastante detalhada. Parabéns.
Excelente conteúdo. Parabéns.
Ta aí uma coisa que às vezes não paramos pra pensar: é necessária adaptação por conta do clima até do ferramental e de sua calibração! Por trás do teclado às vezes somos muito afiados nas críticas, mas há muito trabalho e planejamento envolvidos na produção de aeronaves complexas como essa. Parabéns pelo ótimo conteúdo, Nunão!
Se tudo isso for fruto da compra dos caças e suas compensações, então não fizemos um bom negócio, mas sim um negócio da China.
Meus parabéns!!! Que o Brasil avance cada vez mais com o programa Gripen!
Na última foto fiquei curioso sobre essas antenas, são duas log-periódicas com refletores (pintadas de azul) apontadas uma para a outra.
Seriam para testes de RCS, Radar, Comunicações??
. . “Pra quem acreditou que a Saab iria transferir para Embraer o projeto do aviao para Embraer fabricar o aviao do 0 : todas as peças do aviao caiu do cavalo !!” . . Helen, desconheço que isso tenha feito parte da proposta do Gripen. A Embraer, com equipe de engenheiros treinada na Suécia, faz parte do desenvolvimento do projeto do Gripen F e é responsável pela linha de montagem final / integração dos exemplares que serão produzidos aqui. Nunca teve nada a ver com fabricar o avião do zero. Se alguém um dia achou isso, não foi enganado… Read more »
É… Meu comentário sumiu… Mas imagino do porquê…
O meu comentário também,mais está tudo certo !!!
“mais está tudo certo !!!”
Hellen, analisando que os editores são os donos do aéreo, eles tem todo o direito de apagar o que eles querem, mas olhando pelo lado democrático…
Ué, cadê os outros comentários, inclusive os meus? Fica estranho apagar os comentários, se estivéssemos fora do assunto da matéria tudo bem, mas eu acho que esse não era o caso.
Cor das estruturas Amarelo canário da linha de montagem brasileira!
Sugestivo à nossa bandeira!
Nao sei como os americanos nascidos no Brasil que frequentam aqui não pediram para o prime ser verde igual o F-35 !!! Kkkk
Impressionante como gente que posta na trilogia desacredita o ToT do projeto. Deve ser analfabetismo funcional ou má fé mesmo. Se isso não é um case de sucesso, não sei o que é. Vou voltar pra COPAC e aprender de novo… Parabéns pela matéria. Desmistificou.
Algumas perguntas: se no futuro for necessário criar um ponto de reforço estrutural na asa, teremos essa capacidade? Daqui 15-20 anos poderemos substituir o radar do caça em caso de necessidade, teremos um modelo nacional a disposição? Podemos implementar equipamentos, antenas, algoritmos e biblioteca de sinais próprios na suíte de guerra eletrônica do caça? Nenhuma pergunta / comentário a respeito da diferença nos sistemas das versões suecas e brasileiras? Ok, não conseguimos fabricar os materiais compósito, mas o ferramental da produção é 100% sueco? temos ao menos o conhecimento de como fazer pro futuro, entendemos a natureza do material? Quantas… Read more »
Carcara, algumas respostas possíveis: 1- tendo pessoal e meios que configuram dominio do conhecimento sobre a forma de produção (SAM) , projeto estrutural (Akaer) e integração final das partes (Embraer), acredito que sim. 2- não creio. O desenvolvimento do radar do A-1M, por exemplo, foi uma experiência longa e difícil. Talvez (e friso, talvez) a area de radares da Embraer tenha capacidade de entrar numa parceria com outra empresa internacional para esse eventual substituto que vc deseja. O objeto da matéria aqui é sobre capacidade de manutenção no Brasil, que era um requisito da FAB. 3- O objetivo do programa… Read more »
A pergunta 6 é aquela chapa branca que você faz pra deixar o entrevistado empolgado respondendo uns minutos pra depois soltar um questionamento bomba rsrsrsrs.
Parabéns para a empresa e seus funcionários pelo trabalho realizado. Espero que gerem muitos empregos no Brasil.
Sem querer jogar um copo de agua fria na galera, mais alguns pontos são curiosos 1) Uma matriz transferindo conhecimento critico para sua subsidiaria… o proprio texto ja reconhece esse ponto de inflexão… aonde esta a TOT nisso ai? Deveriam haver clausulas, se quiserem de fato a dita TOT, de garantias que o conhecimento aplicado se difundira através de empresas de fato brasileiras, so mao de obra de gente aplicando rebite não me convence 2) Se voce observar com calma, muitas etapas criticas e cruciais para a fabricação dessas partes, como o desenvolvimento do material composto não são feitos aqui.… Read more »
Foi por isso que falei o pq da Embraer não esta construindo toda fuselagem do avião já que a Saab e a Elbit esta fornecendo a eletrônica e aviônica !!!!! A Embraer nao poderia deixar passar essa oportunidades de aprender a construir uma fuselagem para um aviao supersônico que sera de grande valor para o futuro !!!! Do jeito que a Saab fez transferindo o conhecimento de construção da fuselagem para sua filial esta trocando 6 por meia duzia se é que vc me entendi !!!! Kkkk Mais so de algumas partes do aviao esta sendo construído aqui ja foi… Read more »
Canarinho, resumindo, é mais ou menos uma Helibras 2.0, com a eurocopter “transferindo” tecnologia dela para ela mesmo.
Excelente e bem detalhada matéria. Parabéns Poder Aéreo ‘Nunão’!
Dá pra se ter uma ideia muito boa das diversas atividades que serão desenvolvidas na SAM.
O valor muito mais alto pago pela ToT tem de ser atrelado a um contrato bem elaborado no qual fique bem claro que a transferência de tecnologia tem de ser repassada a empresas brasileiras sem participação societária alguma da empresa transferidora. Justificar que gerou empregos não é nada, qualquer supermercado pode gerar centenas de empregos. Claro que o salário desses empregos criados é bem maior que o salário de empregados no varejo, mas o alto salário a poucos funcionários e o limitado conhecido que adquirem a determinada parte específica do caça não justifica de forma alguma pagarmos um valor muito… Read more »